Minnesota-based Niron Magnetics has opened a commercial pilot plant in Minneapolis.
The plant will develop Niron’s “Clean Earth Magnet,” which is made from iron and nitrogen. The company says the magnets could be used in electric vehicles, wind turbines, audio products, defense and weapons.
According to Niron officials, the company’s magnets are produced in the United States using the world’s first and only process. These are a replacement for most magnets, which are manufactured in China from rare earth materials that may require invasive new mining projects.
“This is a real team effort, both at the legislative government level and obviously at the Niron team level,” Sen. Amy Klobuchar said Thursday at a ribbon-cutting event for the new facility, which was also attended by company officials. and other elected officials. “We will expand our production capacity, invest in new, state-of-the-art equipment, and create 60 good-paying jobs. I can’t wait to see what you do with it.”
MPR News helps cut through the noise and build common understanding. Please support this public resource and keep trustworthy journalism available to everyone.
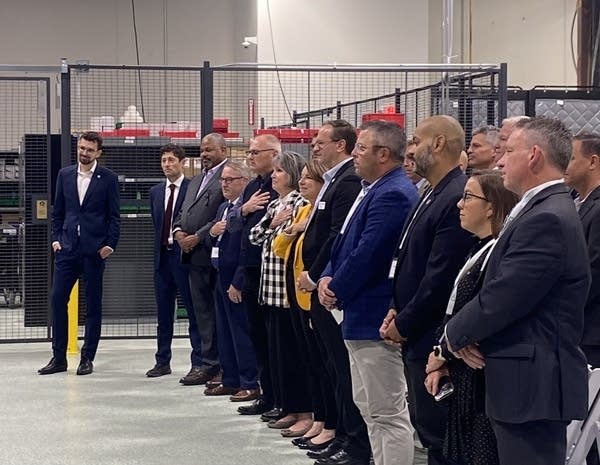
Attendees and speakers at Nylon Magnetics’ ribbon-cutting ceremony included U.S. Sen. Amy Klobuchar, U.S. Reps. Betty McCollum and Pete Stover, and Minneapolis Mayor Jacob Frey.
Annika Best | MPR News
The 70,000-square-foot factory in northeast Minneapolis has the capacity to produce more than 5 tons of magnets per year.
“It’s been a long journey from our early days when we were just a dozen people working in a small lab to where we are today. , now you can actually see it and see it happen. We’re actually making the material, and that’s what I’m most excited about. ” said Frank Johnson, Chief Technology Officer at Niron.
Niron’s magnet manufacturing process begins by creating iron oxide powder. Iron oxide is also called rust. Nylon produces very fine particles of iron oxide, which are passed through a reactor to replace oxygen (oxide) with nitrogen. This produces iron nitride powder, which has magnetic properties.
“We are fighting on a national level to make sure that Minnesota matters, and Mr. Nylon is leading the way,” said Rep. Pete Stover of Minnesota’s 8th District. . “That doesn’t happen without mining the iron ore that makes steel in this country. So it’s a byproduct of steelmaking.”
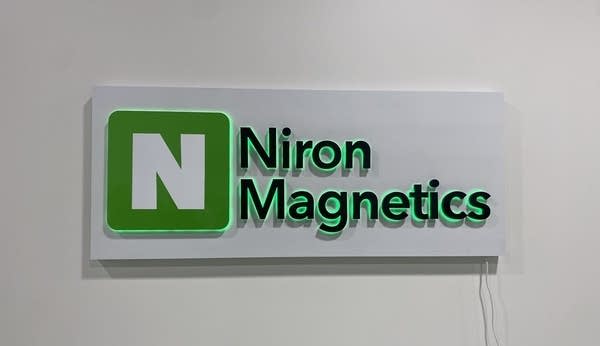
Niron Magnetics opens a commercial pilot plant in Minneapolis.
Annika Best | MPR News
Tom Grainger, Niron’s senior director of business development and investor relations, said iron nitride has been widely discussed in science for decades. A 2011 study by Professor Jian-Ping Wang at the University of Minnesota proved that iron nitride is as high-performing as some hypothesized. This research was funded by the Department of Energy. Niron then developed a process to produce iron nitride.
“We were born in Minnesota,” said Niron CEO Jonathan Rountree.
By-products of magnet manufacturing are salt, water, and steam.
“It’s cleaner to produce, it’s cleaner to recycle, it’s cleaner to dispose of. So it’s a win, win, win,” said U.S. Rep. Betty McCollum of Minnesota’s 4th District.
Niron officials said the company’s magnets can also help keep products such as engines and motors more stable in temperature.
Rountree said being able to offer U.S.-made magnets is an attractive prospect for Niron’s customers.
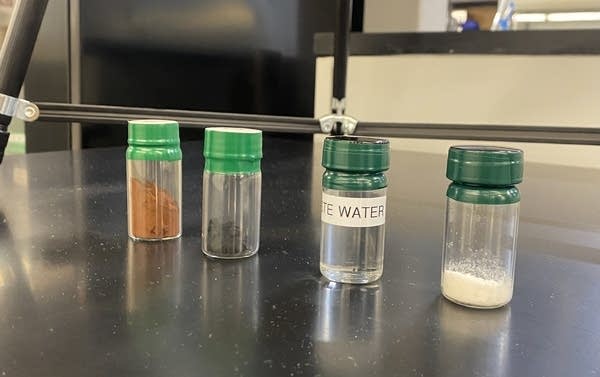
The manufacturing process for Nylon begins with iron oxide powder, which undergoes a chemical process to become iron nitride powder. The two by-products are water and salt.
Annika Best | MPR News
“I think the No. 1 concern for our customers is definitely reliability of supply. They also want more price stability,” Rountree said, adding that “COVID-19 I think many people’s perception of the fragility of the world and the planet has changed due to the impact of this.”
Rountree also noted that the materials to make Nylon magnets are more abundantly available compared to the rare earth materials used in most other magnets.
“The amount of magnets needed will triple over the next 10 years, and there are currently only enough rare earths in the ground from operating sites, factories and mines to double that amount. There will be a very significant shortage of high-performance permanent magnets, and that’s where Nyron comes in,” Rountree said. .
Past customers include General Motors, Magna Powertrain, Samsung Electronics, Harman Audio, Allison Transmission, Volvo Cars and Western Digital.
Earlier this fall, Nylon announced it had selected Sartell, near St. Cloud, for a large-scale manufacturing plant that will produce 1,500 tons of magnets per year.