Sustainable innovation: JLR has committed 65 million pounds to change paint facilities, reducing energy use and emissions, and increasing the demand for custom -made luxury cars. Economic growth: This expansion creates 120 new employment in Slovakia and supports more than 17,000 orders per year. Operation efficiency: Paint shops upgraded in the UK and Slovak saves thousands of tons of CO2 and millions of energy costs every year.
Luxury car manufacturer JLR has invested 65 million pounds to expand and modernize global paint operations, and reconsider to achieve the goal of net zero while responding to soaring demand for personalized luxury cars. We cooperate with the strategy.
Why is it important:
The demand for custom -made paint options for Range Rover and Range Robert Models has been more than doubled since FY2012, and customizations have added £ 70,000 to the Range Rover SVS price.
“Paint shops are very energy -intensive and account for about 80 % of our operating and emissions, so we are the biggest opportunity for us,” said JLR’s highest responsibility. Devon says.
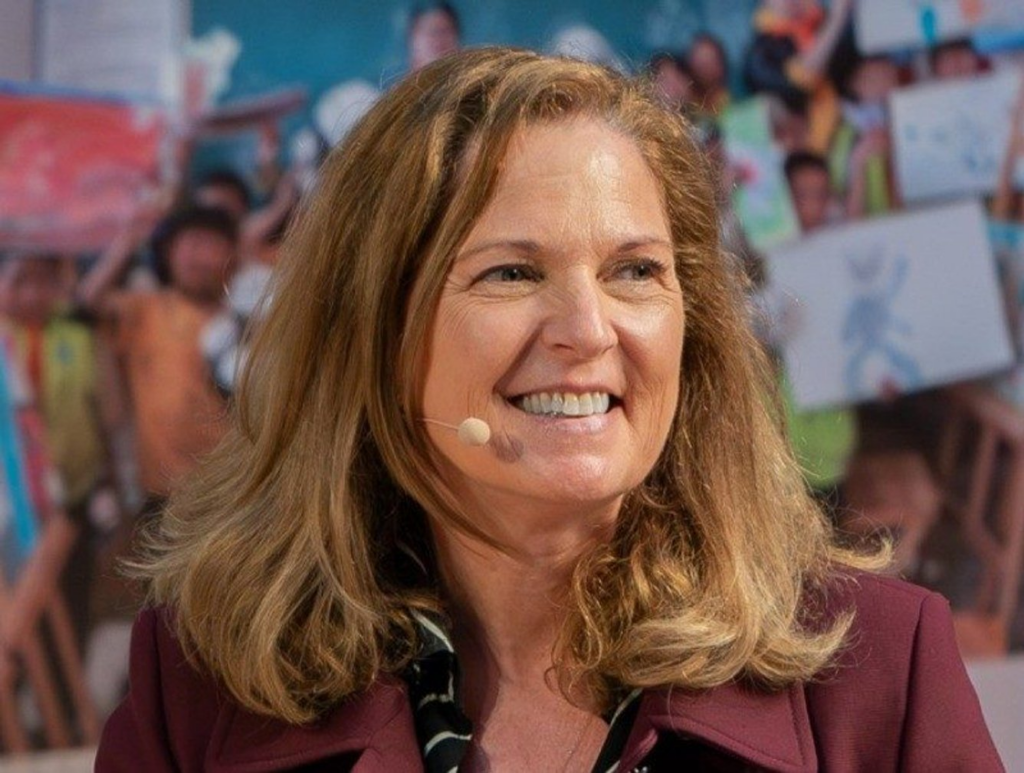
Castle Brom Witch transformation:
The West Midlands facilities will receive 41 million pounds, including £ 26 million, including the state -of -the -art paint booth by 2025. These booths are as follows.
A completely automated spray robot reduces paint waste by 30 % compared to hand -painted. Highly energy -efficient technology to significantly reduce water and energy consumption.
In addition, this extension will introduce SV custom -made painting services for the first time in all JLR brands, supporting luxurious clients that match high -end clients, yachts, or unique preferences.
Related article: JLR embarks on a journey of renewable energy.
Nitra’s Universal Pain Trine:
With a £ 24 million pounds at the JLR’s Slovak Factory, the revolutionary electric paint booth and the oven are cured, marking important steps for zero carbon operation.
This upgrade avoids 500 tons of CO2 every year, equivalent to 2,200 barrel oil. The new heat exchanger and smart oven control are expected to save 2,250 tons of CO2 each year and reduce operating costs by 750,000 pounds.
“By enhancing abilities, you can meet the increase in demand from the Range Rover clients and expand this service to other brands,” said JLR spokeswoman.
Future headline:
The improved facility is the first vehicle of the Nitra Plant’s Universal Pain Trine, which will be debuted in 2026, and is expected to support more than 17,000 new edition orders per year.
JLR’s efforts reflect a wide range of commitments rather than reducing the impact of the most carbon -intensive process in the automotive industry, maintaining the position of a luxury car personalization leader.
Follow the Linkedin ESG news